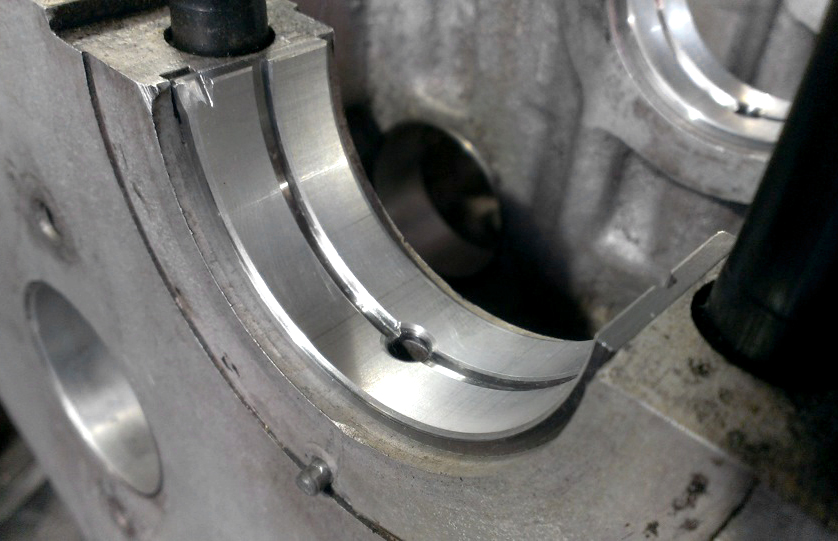
In all internal combustion engines, the crankshaft and connecting rods rotate in special bearings - liners. Read about what a crankshaft liner is, what functions it performs, what types of liners are and how they are arranged, as well as the correct selection of new liners for repair - read the article.
What are crankshaft liners?
The crankshaft liner is a part of the crank mechanism of an internal combustion engine, a plain bearing that reduces friction losses and jamming of parts at the points of contact of the crankshaft with the bed of the engine block and crankshaft with piston connecting rods. The use of plain bearings is due to difficult conditions and high loads, under which rolling bearings (ball or roller) would work inefficiently and would have a short resource. Today, most power units use liners, and only on some low-power one- and two-cylinder engines, rolling bearings are used as crankshaft supports.
The crankshaft liners have several basic functions:
• Reduction of friction forces at the point of contact of the crankshaft, cylinder block supports and connecting rods;
• Transfer of forces and torques arising during engine operation - from connecting rods to the crankshaft, from the crankshaft to the engine block, etc.;
• Proper distribution of oil (formation of an oil film) on the surfaces of rubbing parts;
• Correct alignment and positioning of parts relative to each other.
The crankshaft liners play an important role in the operation of the power unit, but at the same time they are quite simple in terms of design.
Types and characteristics of crankshaft liners
Crankshaft plain bearings are divided into types according to the place of installation, purpose and repair dimensions.
At the place of installation, there are two types of liners:
•Indigenous;
• Connecting rods.
Main plain bearings are installed in the crankshaft bed in the engine block and cover the main journals of the crankshaft, ensuring its free rotation. Connecting rod plain bearings are installed in the lower head of the connecting rod and cover the connecting rod journal of the crankshaft.
Also, inserts are divided into two groups according to their purpose:
• Conventional - provide only a reduction in friction forces at the points of contact of parts;
• Locking main - additionally provide fixation of the crankshaft in the bed, preventing its axial displacement.
Conventional plain bearings are flat, thin-walled half-rings. Locking bearings can be made in the form of thrust half-rings (which are used in a set with a flat liner) and liners with collars; Half rings are installed at the end of the engine, collar liners are mounted on one or two supports of the crankshaft bed.
The crankshaft liners wear out during operation and must be replaced, the crankshaft journals are also subject to wear, which leads to an increase in the gap between the rubbing parts. If you install new liners of the same thickness as the old ones, the gap will remain too large, which is fraught with knocking and even more intense wear. To avoid this, liners of the so-called repair dimensions are used - a slightly increased thickness that compensates for the wear of the crankshaft journals. New liners have a size of 0.00, repair liners are produced with an increase in thickness by 0.25, 0.5, 0.75, 1.0, 1.25, 1.5 mm, such inserts are designated respectively +0.25, +0.5, etc.
The design of the crankshaft liners
The crankshaft plain bearing is composite, contains two metal flat half rings that completely cover the crankshaft journal (top and bottom). There are several elements in this part:
• Holes (one or two) for passing oil into the oil channels in the crankshaft and connecting rod;
• Locks in the form of spikes or grooves for pins for fixing the bearing in the crankshaft bed support or in the lower connecting rod head;
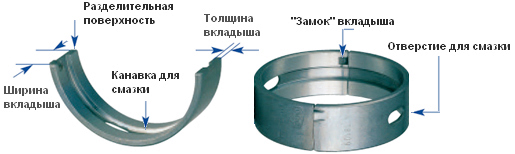
• Longitudinal groove for oil supply to the hole (performed only on the liner located on the side of the channel - this is the lower main liner and the upper connecting rod liner);
• In collar thrust liners - side walls (collars) for fixing the bearing and limiting the axial movement of the crankshaft.
The liner is a multilayer structure, the basis of which is a steel plate with an anti-friction coating applied to its working surface. It is this coating that provides a reduction in friction and a long service life of the bearing, it is made of soft materials and, in turn, can also be multilayered. Due to its lower softness, the liner coating absorbs microscopic particles of crankshaft wear, prevents jamming of parts, scuffing, etc.
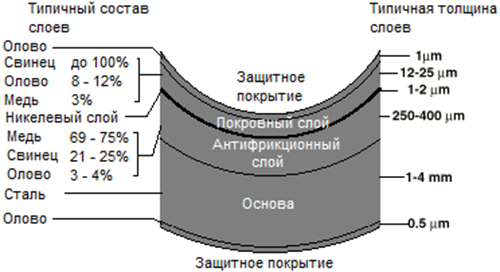
By design, crankshaft liners are divided into two main groups:
•Bimetal;
• Trimetallic.
Bimetallic bearings are arranged most simply. They are based on a steel strip with a thickness of 0.9-4 mm (depending on the type and purpose of the part, the main bearings are thicker, the connecting rods are thinner), on which an antifriction layer with a thickness of 0.25-0.4 mm is applied. solid lubricant) up to 75%, may also contain small amounts of nickel, cadmium, zinc and other metals.
In addition to the main anti-friction coating, trimetallic liners have a cover layer with a thickness of 0.012-0.025 mm (12-25 μm), which provides protective properties (fights corrosion and excessive wear of the base layer) and improves the antifriction qualities of the bearing. This coating is made of lead-tin-copper alloy with a lead content of 92-100%, tin up to 12% and copper not more than 3%.
Also, additional layers may be present in plain bearings:
• The top protective layer of tin is a pure tin coating with a thickness of only 0.5-1 microns, which provides protection against corrosion, grease and contamination during transportation, installation and running-in of the liner;
• The lower protective layer of tin is the same layer applied on the outside of the liner (facing the crankshaft supports or the inside of the connecting rod head);
• Nickel sublayer (nickel barrier, gasket) - a thin, no more than 1-2 micron layer of nickel between the main antifriction coating and the coating layer. This layer prevents the diffusion of tin atoms from the coating layer into the main one, which ensures the constancy of the chemical composition of the main antifriction coating. In the absence of a nickel barrier in the main coating, the concentration of tin may increase, which leads to negative changes in the characteristics of the bearing.
The considered structure of plain bearings is not a standard, many manufacturers offer their own unique schemes and designs. For example, the main antifriction alloy can be applied to the steel base not directly, but through an additional sublayer of aluminum or copper alloy, the coating layer can have a variety of compositions, including lead-free, etc.
Issues of selection and replacement of crankshaft liners
When selecting plain bearings, it is necessary to start from the engine model, the wear of the mating parts and the presence of repair liners. As a rule, liners are made for one model range or even one engine model, so it is impossible to replace them with parts from another motor (with rare exceptions). Also, you can not use liners without taking into account the wear of the crankshaft journals, otherwise the repair will turn into even greater problems.
Before choosing the repair size of bearings, it is necessary to determine the wear of the crankshaft journals and other related parts (beds, connecting rod heads, although they are less susceptible to wear). Usually, the wear of the necks occurs unevenly, some of them wear out more intensively, some less, but a set of identical liners is bought for repair, so all necks must be ground to the same size. The choice of the value to which the crankshaft journals will grind depends on the availability of bearings of certain repair sizes suitable for this particular engine. For motors with low mileage, repair sizes of +0.25 or +0.5 are selected, for motors with significant mileage, grinding to a repair size of +1.0 may be required, in old motors even more - up to +1.5. Therefore, for new engines, liners of three or four repair sizes (up to +0.75 or +1.0) are usually produced, and for old ones, liners up to +1.5 can be found.
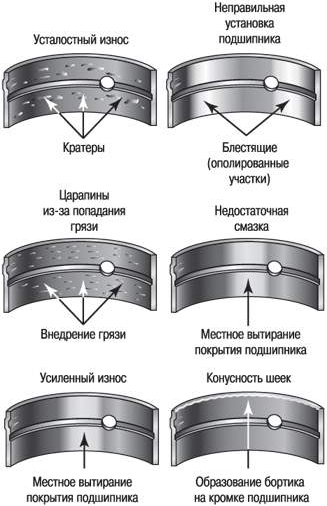
The repair size of the crankshaft liners should be such that when assembling the engine between the crankshaft journal and the bearing surface, there is a gap in the range of 0.03-0.07 mm.
With the right choice of plain bearings for the crankshaft, the engine, even with high mileage, will work efficiently and efficiently in various modes.
Post time: Aug-22-2023