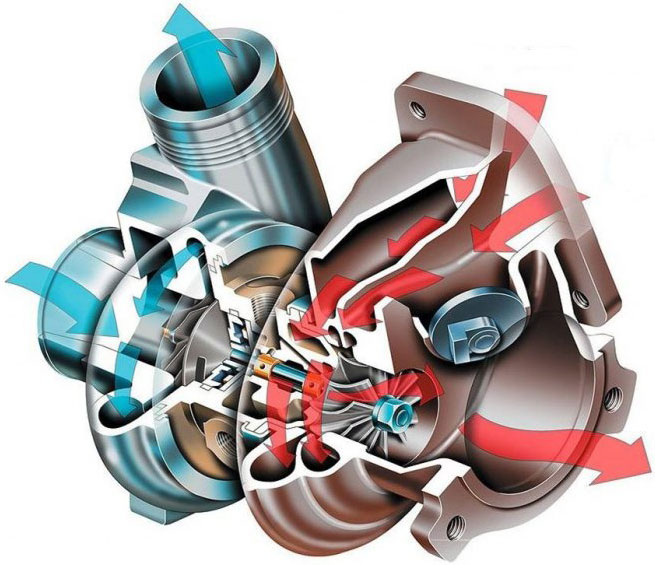
To increase the power of internal combustion engines, special units - turbochargers - are widely used. Read about what a turbocharger is, what types these units are, how they are arranged and on what principles their work is based, as well as about their maintenance and repair, in the article.
What is a turbocharger?
The turbocharger is the main component of the aggregate pressurization system of internal combustion engines, a unit for increasing the pressure in the intake tract of the engine due to the energy of the exhaust gases.
The turbocharger is used to increase the power of an internal combustion engine without radical interference in its design. This unit increases the pressure in the intake tract of the engine, providing an increased amount of fuel-air mixture to the combustion chambers. In this case, combustion occurs at a higher temperature with the formation of a larger volume of gases, which leads to an increase in pressure on the piston and, as a result, to an increase in torque and engine power characteristics.
The use of a turbocharger allows you to increase engine power by 20-50% with a minimal increase in its cost (and with more significant modifications, power growth can reach 100-120%). Due to their simplicity, reliability and efficiency, turbocharger-based pressurization systems are widely used on all types of internal combustion engine vehicles.
Types and characteristics of turbochargers
Today, there is a wide variety of turbochargers, but they can be divided into groups according to their purpose and applicability, the type of turbine used and additional functionality.
According to the purpose, turbochargers can be divided into several types:
• For single-stage pressurization systems - one turbocharger per engine, or two or more units operating on several cylinders;
•For series and series-parallel inflation systems (various variants of Twin Turbo) - two identical or different units operating on a common group of cylinders;
• For two-stage pressurization systems, there are two turbochargers with different characteristics, which work in pairs (sequentially one after the other) for one group of cylinders.
The most widely used are single-stage pressurization systems built on the basis of a single turbocharger. However, such a system may have two or four identical units - for example, in V-shaped engines, separate turbochargers are used for each row of cylinders, in multi-cylinder engines (more than 8) four turbochargers can be used, each of which works on 2, 4 or more cylinders. Less common are two-stage pressurization systems and various variations of Twin-Turbo, they use two turbochargers with different characteristics that can only work in pairs.
According to applicability, turbochargers can be divided into several groups:
• By engine type - for gasoline, diesel and gas power units;
• In terms of engine volume and power - for power units of small, medium and high power; for high-speed engines, etc.
Turbochargers can be equipped with one of two types of turbine:
• Radial (radial-axial, centripetal) - the flow of exhaust gases is fed to the periphery of the turbine impeller, moves to its center and is discharged in the axial direction;
• Axial - the flow of exhaust gases is supplied along the axis (to the center) of the turbine impeller and is discharged from its periphery.
Today, both schemes are used, but on small engines you can often find turbochargers with a radial-axial turbine, and on powerful power units, axial turbines are preferred (although this is not the rule). Regardless of the type of turbine, all turbochargers are equipped with a centrifugal compressor - in it air is supplied to the center of the impeller and removed from its periphery.
Modern turbochargers can have different functionality:
• Double inlet - the turbine has two inputs, each of them receives exhaust gases from one group of cylinders, this solution reduces pressure drops in the system and improves boost stability;
• Variable geometry - the turbine has movable blades or a sliding ring, through which you can change the flow of exhaust gases to the impeller, this allows you to change the characteristics of the turbocharger depending on the engine operating mode.
Finally, turbochargers differ in their basic performance characteristics and capabilities. Of the main characteristics of these units should be highlighted:
• The degree of pressure increase - the ratio of air pressure at the outlet of the compressor to the air pressure at the inlet, lies in the range of 1.5-3;
• Compressor supply (air flow through the compressor) - the mass of air passing through the compressor per unit of time (second) lies in the range of 0.5-2 kg / s;
• The operating speed range ranges from several hundred (for powerful diesel locomotives, industrial and other diesel engines) to tens of thousands (for modern forced engines) revolutions per second.The maximum speed is limited by the strength of the turbine and compressor impellers, if the rotation speed is too high due to centrifugal forces, the wheel can collapse. In modern turbochargers, the peripheral points of the wheels can rotate at speeds of 500-600 or more m / s, that is, 1.5-2 times faster than the speed of sound, this causes the occurrence of the characteristic whistle of the turbine;
• The operating / maximum temperature of the exhaust gases at the inlet to the turbine lies in the range of 650-700 ° C, in some cases reaches 1000 ° C;
• The efficiency of the turbine / compressor is usually 0.7-0.8, in one unit the efficiency of the turbine is usually less than the efficiency of the compressor.
Also, the units differ in size, type of installation, the need to use auxiliary components, etc.
Turbocharger design
In general, the turbocharger consists of three main components:
1.Turbine;
2.Compressor;
3.Bearing housing (central housing).
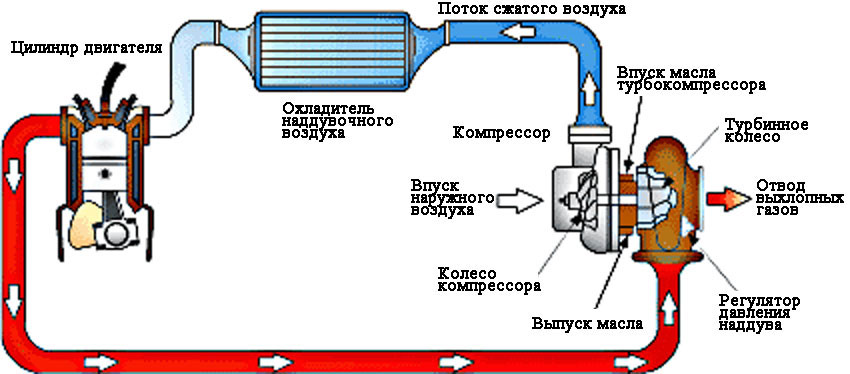
Typical diagram of the internal combustion engine aggregate air pressurization system
A turbine is a unit that converts the kinetic energy of the exhaust gases into mechanical energy (in the torque of the wheel), which ensures the operation of the compressor. A compressor is a unit for pumping air. The bearing housing connects both units into a single structure, and the rotor shaft located in it ensures the transfer of torque from the turbine wheel to the compressor wheel.
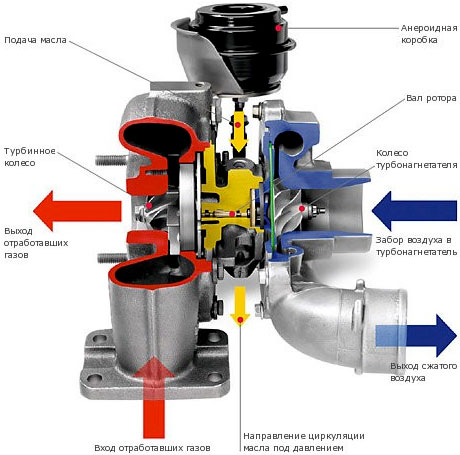
Turbocharger section
The turbine and compressor have a similar design. The basis of each of these units is the cochlear body, in the peripheral and central parts of which there are pipes for connection to the pressurization system. In the compressor, the inlet pipe is always in the center, the exhaust (discharge) is on the periphery. The same arrangement of pipes for axial turbines, for radial-axial turbines, the location of the pipes is the opposite (on the periphery - intake, in the center - exhaust).
Inside the case there is a wheel with blades of a special shape. Both wheels - turbine and compressor - are held by a common shaft that passes through the bearing housing. The wheels are solid-cast or composite, the shape of the turbine wheel blades ensures the most efficient use of exhaust gas energy, the shape of the compressor wheel blades provides the maximum centrifugal effect. Modern high-end turbines can use composite wheels with ceramic blades, which have a low weight and have better performance. The size of the wheels of turbochargers of automobile engines is 50-180 mm, powerful locomotive, industrial and other diesel engines are 220-500 mm or more.
Both housings are mounted on the bearing housing with bolts through seals. Plain bearings (less often rolling bearings of a special design) and O-rings are located here. Also in the central housing there are oil channels for lubricating the bearings and shaft, and in some turbochargers and the cavity of the water cooling jacket. During installation, the unit is connected to the engine lubrication and cooling systems.
Various auxiliary components can also be provided in the design of the turbocharger, including parts of the exhaust gas recirculation system, oil valves, elements for improving the lubrication of parts and their cooling, control valves, etc.
Turbocharger parts are made of special steel grades, heat-resistant steels are used for the turbine wheel. Materials are carefully selected according to the coefficient of thermal expansion, which ensures the reliability of the design in various operating modes.
The turbocharger is included in the air pressurization system, which also includes intake and exhaust manifolds, and in more complex systems - an intercooler (charge air cooling radiator), various valves, sensors, dampers and pipelines.
The principle of operation of the turbocharger
The functioning of the turbocharger comes down to simple principles. The turbine of the unit is introduced into the exhaust system of the engine, the compressor - into the intake tract. During the operation of the engine, the exhaust gases enter the turbine, hit the wheel blades, giving it some of its kinetic energy and causing it to rotate. The torque from the turbine is directly transmitted to the compressor wheels via the shaft. When rotating, the compressor wheel throws air to the periphery, increasing its pressure - this air is supplied to the intake manifold.
A single turbocharger has a number of disadvantages, the main of which is turbo delay or turbo pit. The wheels of the unit have mass and some inertia, so they cannot instantly spin up when the speed of the power unit increases. Therefore, when you press the gas pedal sharply, the turbocharged engine does not accelerate immediately - there is a short pause, a power failure. The solution to this problem is special turbine control systems, turbochargers with variable geometry, series-parallel and two-stage pressurization systems, and others.
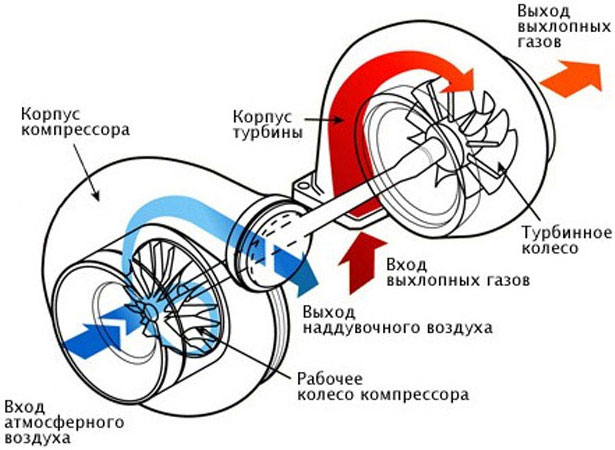
The principle of operation of the turbocharger
Issues of maintenance and repair of turbochargers
The turbocharger needs minimal maintenance. The main thing is to change the engine oil and oil filter in time. If the engine can still run on old oil for some time, then it can become deadly for the turbocharger - even a slight deterioration in the quality of the lubricant at high loads can lead to jamming and destruction of the unit. It is also recommended to periodically clean the turbine parts from carbon deposits, which requires its disassembly, but this work should be performed only with the use of special tools and equipment.
A faulty turbocharger is in most cases easier to replace than to repair. For replacement, it is necessary to use a unit of the same type and model that was installed on the engine earlier. Installation of a turbocharger with other characteristics may disrupt the operation of the power unit. It is better to trust the selection, installation and adjustment of the unit to specialists - this guarantees the correct execution of work and the normal operation of the engine. With the correct replacement of the turbocharger, the engine will regain high power and will be able to solve the most difficult tasks.
Post time: Aug-21-2023