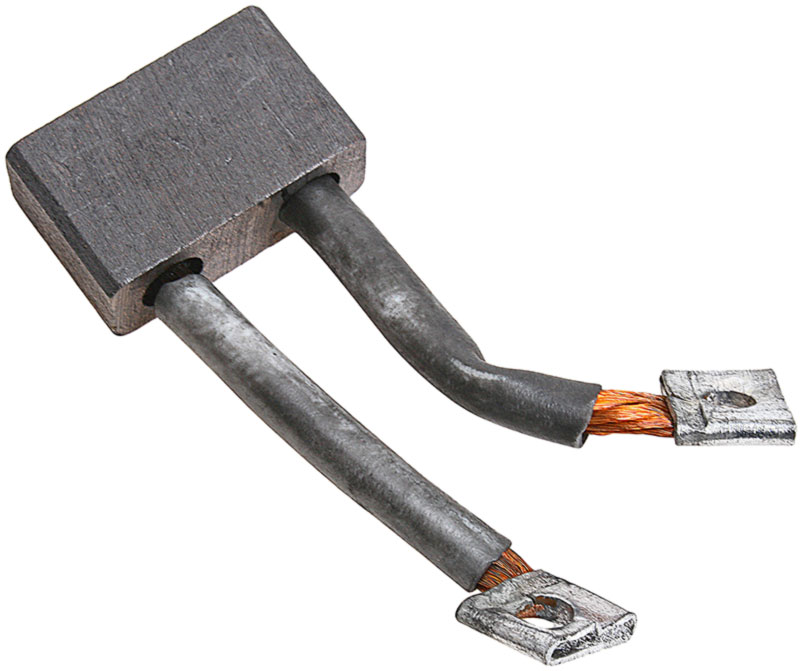
Every modern car has an electric starter that provides the start of the power unit. An important component of the starter is a set of brushes that supply electric current to the armature. Read about starter brushes, their purpose and design, as well as diagnostics and replacement in the presented article.
Purpose and role of brushes in the electric starter
In most modern vehicles equipped with internal combustion engines, the task of starting the power unit is solved using an electric starter. Over the past half century, starters have not undergone significant changes: the basis of the design is a compact and simple DC electric motor, which is supplemented by a relay and a drive mechanism. The starter motor consists of three main components:
- Body assembly with stator;
-Anchor;
- Brush assembly.
The stator is the fixed part of the electric motor. The most commonly used are electromagnetic stators, in which the magnetic field is created by field windings. But you can also find starters with stators based on conventional permanent magnets. The armature is the moving part of the electric motor, it contains windings (with pole tips), a collector assembly and drive parts (gears). The rotation of the armature is provided by the interaction of magnetic fields formed around the armature and stator windings when an electric current is applied to them.
The brush assembly is an electric motor assembly that provides sliding contact with a movable armature. The brush assembly consists of several main parts - brushes and a brush holder that holds the brushes in working position. The brushes are pressed against the armature collector assembly (it consists of a number of copper plates that are the contacts of the armature windings), which ensures a constant supply of current to the armature windings during its rotation.
Starter brushes are important and critical components that should be described in more detail.
Types and design of starter blades
Structurally, all starter brushes are fundamentally the same. A typical brush consists of two main parts:
- Brush molded from soft conductive material;
- Flexible conductor (with or without terminal) to supply current.
The brush is a parallelepiped molded from a special conductive material based on graphite. Currently, starter brushes are made of two main materials:
- Electrographite (EG) or artificial graphite. Material obtained by pressing and roasting from coke or other conductive materials based on carbon and hydrocarbon binder;
- Composites based on graphite and metal powder. The most commonly used copper-graphite brushes are pressed from graphite and copper powder.
The most widely used copper-graphite brushes. Due to the inclusion of copper, such brushes have less electrical resistance and are more resistant to wear. Such brushes have several drawbacks, the main of which is the increased abrasive effect, which leads to increased wear of the armature manifold. However, the operating cycle of the starter is usually short (from a few tens of seconds to several minutes a day), so the wear of the manifold is slow.
One or two flexible conductors of large cross-section are rigidly fixed in the body of the brush. Conductors are copper, stranded, woven from several thin wires (which provides flexibility). On brushes for low-power starters, only one conductor is usually used, on brushes for high-power starters, two conductors are fixed on opposite sides of the brush (for uniform current supply). Installation of the conductor is usually carried out using a metal sleeve (piston). The conductor can be either bare or insulated - it all depends on the design of a particular starter. A terminal can be located at the end of the conductor for ease of installation. The conductors must be flexible, which allows the brush to change position during wear and during starter operation, without losing contact with the manifold.
Several brushes are used in the starter, usually their number is 4, 6 or 8. In this case, half of the brushes are connected to the "ground", and the other half to the stator windings. This connection ensures that when the starter relay is turned on, current is simultaneously applied to the stator windings and armature windings.
The brushes are oriented in the brush holder in such a way that at each moment of time the current is applied to certain armature windings. Each brush is pressed against the manifold by means of a spring. The brush holder, together with the brushes, is a separate unit, which, if it is necessary to repair or replace the brushes, can be dismantled and easily installed in place.
In general, starter brushes are very simple, so they are reliable and durable. However, they also need periodic maintenance and repair.
Issues of diagnostics and repair of starter brushes
During operation, starter brushes are subjected to constant wear and significant electrical loads (at the time of starting the engine, a current of 100 to 1000 or more amperes flows through the brushes), so over time they decrease in size and collapse. This can lead to a loss of contact with the collector, which means a deterioration in the operation of the entire starter. If the starter begins to work worse over time, does not provide the necessary angular velocity of rotation of the crankshaft or does not turn on at all, then you should check its relay, the condition of the electrical contacts and, finally, the brushes. If everything is in order with the relay and contacts, and the starter does not work well even when connected to the battery, bypassing the relay, then the problem should be sought in the brushes.
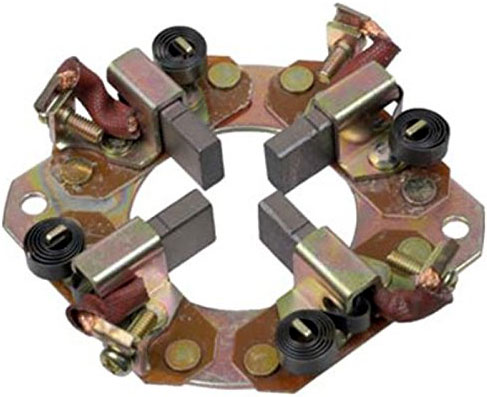
To diagnose and replace brushes, the starter should be dismantled and disassembled, in general, disassembly is performed as follows:
- Unscrew the bolts holding the rear cover of the starter;
- Remove the cover;
- Remove all seals and clamps (usually there are two O-rings, a clamp and a gasket in the starter);
- Carefully remove the brush holder from the armature manifold. In this case, the brushes will be pushed out by springs, but nothing terrible will happen, since the parts are held by flexible conductors.
Now you need to make a visual inspection of the brushes, assess the degree of wear and integrity. If the brushes have excessive wear (have a length shorter than recommended by the manufacturer), cracks, kinks or other damage, then they should be replaced. Moreover, the complete set of brushes changes immediately, since the old brushes may soon fail and repairs will have to be performed again.
Dismantling of brushes is carried out depending on their type of fastening. If the conductors are simply soldered, then you should use a soldering iron. If there are terminals on the conductors, then dismantling and installation is reduced to unscrewing / screwing in screws or bolts. Installation of new brushes is carried out in reverse order, while it is necessary to monitor the reliability of electrical contacts.
After replacing the brushes, the starter is assembled in reverse order, and the entire unit is installed in its regular place. The new brushes have a flat working part, so they will be "run-in" for several days, at which time the starter should be avoided at increased loads. In the future, the starter brushes do not require special care and maintenance.
Post time: Aug-27-2023